Industrial pumps play a pivotal role in ensuring seamless and efficient operations in countless industries. From manufacturing to water treatment, these machines form the backbone of critical processes. Their ability to maintain steady performance under demanding conditions directly impacts your productivity and operational reliability. Industrial pumps, when chosen and maintained correctly, ensure processes remain uninterrupted, reduce downtime, and optimize overall efficiency.
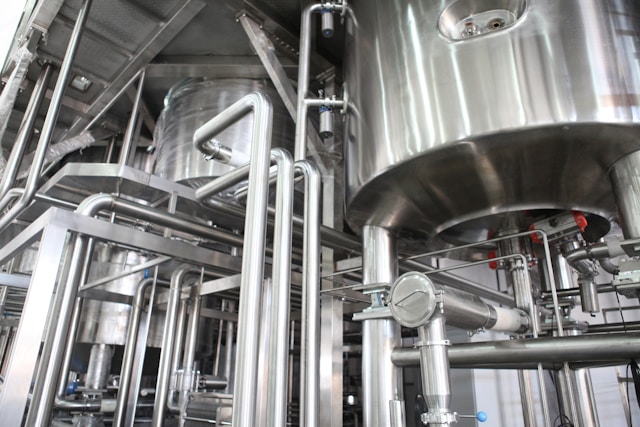
Enhanced Durability
Durability is crucial when you rely on equipment to operate continuously in harsh environments. Industrial pumps are engineered to withstand demanding conditions, minimizing the risk of unexpected failures. For heavy-duty industrial applications, a 12-inch slurry pump benefits significantly from these durable materials. The materials used in industrial pumps – such as stainless steel, cast iron, or specialized alloys – are designed to resist corrosion, abrasion, and high pressures. This resilience ensures the pumps continue performing reliably even under extreme conditions.
● Extending Lifespan
Durable pumps require less frequent replacements, saving you time and resources. With proper maintenance, these pumps deliver consistent performance over many years, ensuring you get the most out of your investment.
Precision Flow Control
Accurate flow control is essential for maintaining the integrity of many industrial processes. Industrial pumps excel in delivering precise flow rates tailored to your specific needs.
When your operations depend on consistent material movement, precise flow control is indispensable. Industrial pumps, equipped with advanced control mechanisms, ensure that materials such as liquids, slurries, or chemicals are transferred at the exact rate required. This precision minimizes variability and helps you maintain stable process conditions.
● Enhancing Product Quality
Variations in flow rates can lead to inconsistencies in your end products. By utilizing pumps designed for accurate and consistent delivery, you can ensure that your products meet exact specifications, reducing waste and improving overall quality. Consistent performance from your pumps translates directly into fewer errors and greater customer satisfaction.
Energy Efficiency
Energy costs can account for a significant portion of your operational expenses. Industrial pumps designed with efficiency in mind reduce energy consumption and help you manage costs more effectively.
● Reducing Operational Costs
Energy-efficient pumps incorporate features such as variable frequency drives (VFDs) and optimized impeller designs. These innovations allow the pumps to adjust their performance based on real-time demands, ensuring you’re not wasting energy during lower-demand periods.
● Lowering Environmental Impact
By reducing energy consumption, industrial pumps help you decrease your environmental footprint. Efficient energy use supports sustainability goals while also complying with increasingly stringent regulations. Opting for energy-efficient pumps benefits both your bottom line and your commitment to sustainability.
Improved System Integration
Industrial processes often rely on a combination of equipment working seamlessly together. Modern industrial pumps are designed for easy integration into complex systems.
Automation has become essential for enhancing efficiency and reliability. Industrial pumps equipped with smart sensors and remote monitoring capabilities can communicate with other system components. This integration allows you to automate operations and gain real-time insights, improving overall process control.
● Simplifying Maintenance
Integrated pumps can provide diagnostic data that helps you identify issues before they escalate. Alerts and performance metrics from the pump’s monitoring system enable you to address potential problems proactively, reducing downtime and maintenance costs.
Versatility in Applications
One of the standout features of industrial pumps is their ability to handle a wide range of materials and operating conditions. This adaptability makes them indispensable across various industries.
Industrial pumps are designed to transfer liquids, gases, and even solid-laden slurries. Whether you’re working in chemical processing, food and beverage, or wastewater management, you’ll find pumps tailored to your specific needs, ensuring smooth operation regardless of material type.
From high-pressure settings to extreme temperatures, industrial pumps operate reliably in demanding conditions. This versatility ensures you can rely on a single type of pump or a cohesive system to meet diverse operational requirements.
Minimized Downtime
Operational downtime can disrupt your processes and result in significant financial losses. Industrial pumps are engineered to maximize uptime, ensuring your systems remain operational when you need them most.
Many industrial pumps are designed for easy disassembly and reassembly, enabling quicker repairs. Spare parts are readily available, and modular designs simplify component replacement, so you can minimize disruptions to your operations.
● Increasing Process Resilience
Reliable pump performance allows your processes to continue uninterrupted. By choosing pumps with proven reliability and robust designs, you reduce the likelihood of unexpected breakdowns and enhance overall system resilience.
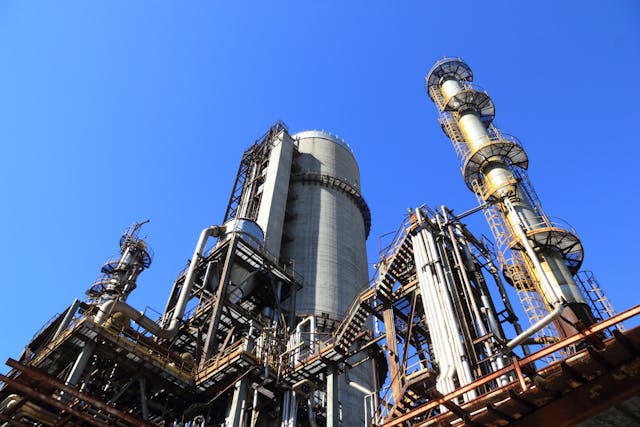
Industrial pumps are more than just functional components – they are critical enablers of process reliability and efficiency. By offering precision flow control, energy efficiency, durability, and seamless integration, they empower you to optimize your operations and achieve greater consistency in performance. The benefits extend far beyond the equipment itself, impacting your energy consumption, product quality, and overall operational costs.